Co-Extrusion Blow Molding Machine
Multilayer Co-Extrusion Material Structure
Extrusion blow molding is one of the most common technologies widely applied in the production of plastic containers for decades. By the requirement from the consumer market, the technology has improved in machinery performance and container structure to overcome the price competition, environmental issues, and logistic challenges.
Atenplast has accumulated over 30 years of experience in the Co-Extrusion Blow molding machine manufacture.
Main technologies on our Co-extrusion Blow Molding Machine
- A unique design of screw can use regrind co-extruded material into the middle layer
- Co-extrusion multilayer accumulator head with PWDS (Parison wall distribution System)
- Piston type power Accumulator
- Foaming formulation
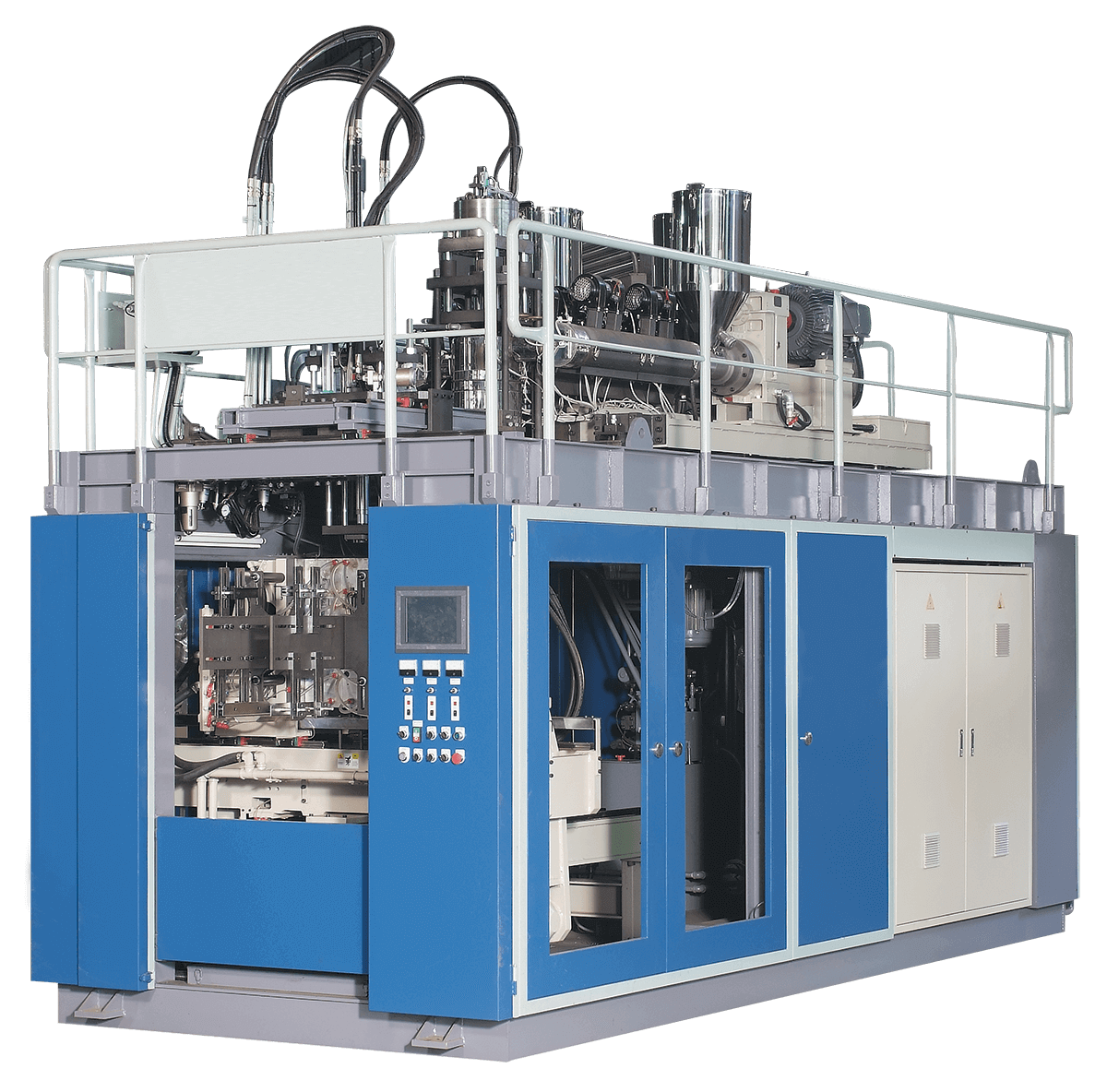
Our Models
Container < 30L
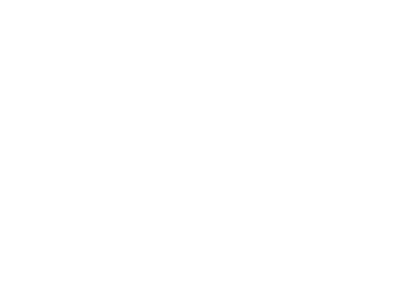
ECM Series
All electrical continuous model
Small bottles & containers
Jerry cans & handle ware bottles
Container < 60L
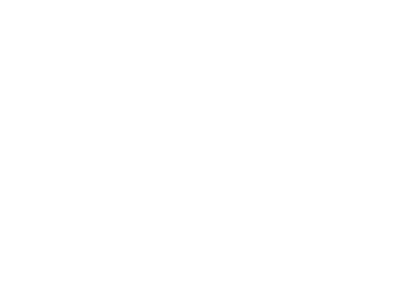
HCM Series
Hybrid hydraulic continuous model
Small bottles & containers
Jerry cans & handle ware bottles
Container up to 3000L
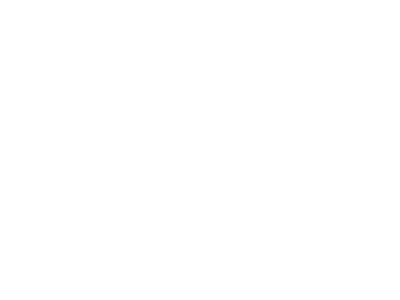
HAM Series
Hydraulic Accumulator Head model
Large volume containers
IBC Tank, Chemical drums, water tanks, Road barrier, Plastic pallet, Furniture
Automobile parts.
Key technologies in our blow molding machine
Multilayer Co-Extrusion Material Structure
Compared to the traditional single layer structure, the multilayer structure container has more functional applications. But the most attractive point is, it saves more material cost by reusing lots percentage of regrind material into the middle layer of the container. The container has even better strength, and the same outlook like a single layer container produced from virgin material.
Features
Common multilayer structure application
Example of 6 layers structure container
Layer 1 (outer): Virgin resin with color masterbatch
Layer 2 : Adhesive material
Layer 3 : Barrier material (Nylon / EVOH)
Layer 4 : Adhesive material
Layer 5 : Regrind material
Layer 6 (inner ) : Virgin Material
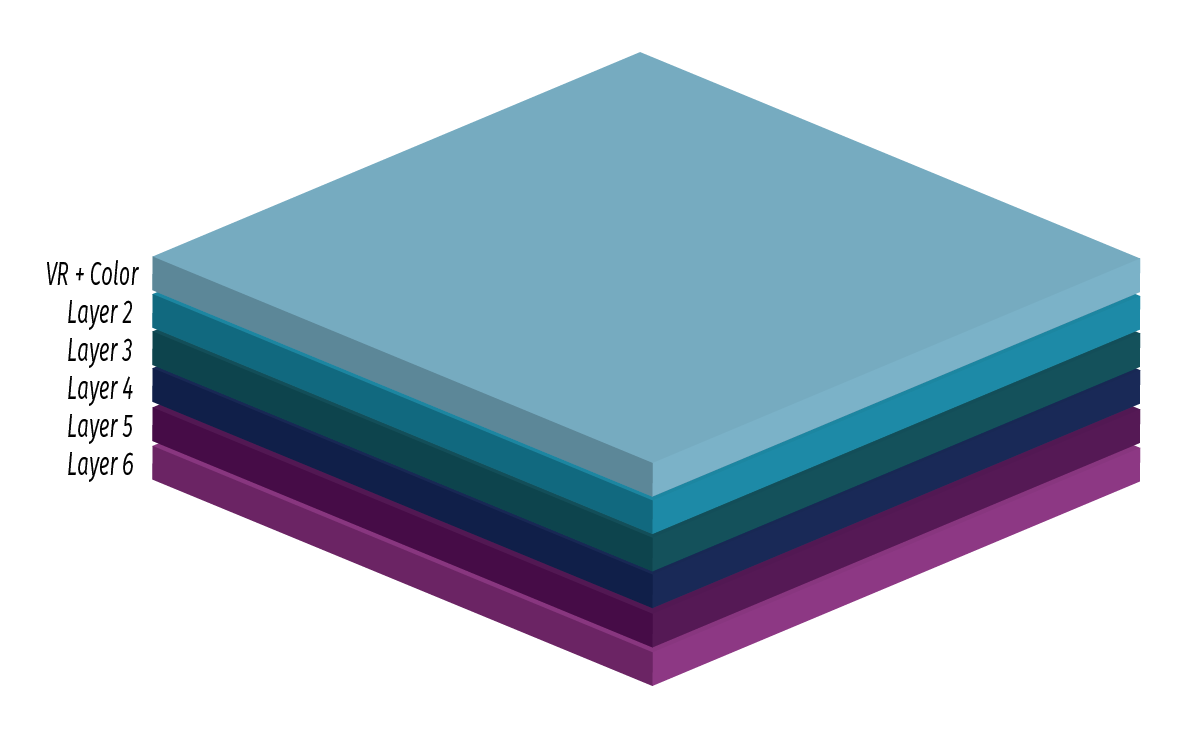
VR: Virgin material. Ex: PP/HDPE/LDPE/PETG/PC/ABS
RM: Resin with masterbatch. Ex: Color masterbatch, CaCO3
Barrier : Special material of barrier purpose. Ex: EVOH/NYLON
RGD: Regrind material
AD: Adhensive material
Energy saving system
Energy consumption is a direct factor to the manufacturing cost and product margin. Some customers made the wrong decision of purchasing a machine without considering how important this factor is. Some machine maker doesn't focus on this issue because the solution will increase the machine price and make the sale more difficult. Atenplast knows this factor is one of the keys to success, so we made a lot of effort on the improvement of the energy issue.
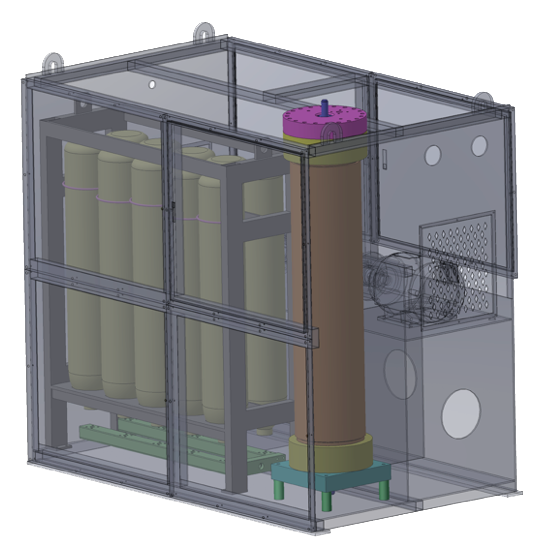
Hydraulic power accumulator system
Features
Extrusion foaming formula
The material is another important issue. With multilayer structure, various formulas can apply in different purpose. The foaming formula is absolutely the new technology and most attractive method for the next generation of the extrusion blow molding process. It will decrease the product weight without reducing the density. And the impact resistance of the container could be even better.
Compare our table by choosing your bottle volume to know how much cost you can save on production efficiency by using our ECM & HCM series.
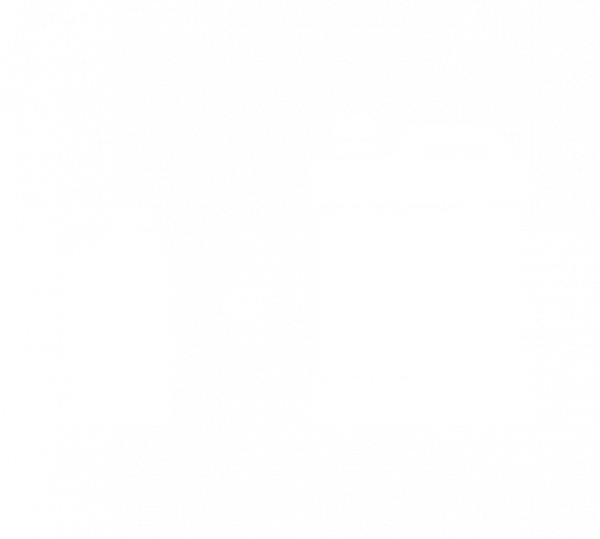
2L
90g
3L
150g
5L
210g
10L
500g
30L
2000g
2L (90g)
3L (150g)
5L (210g)
10L (500g)
30L (2000g)
- Average cycle time is calculated by the container weigh which is based on the experience of Atenplast without post cooling device.
- The table is considered the situation under single cavity per mold. Multi-cavities could make the difference larger.
- Monthly production is considered with 600 hours continual production
- Electricity cost is considered as USD0.06/kWh, which is average industrial electricity cost of 2017 in USA
- Labor cost is considered as USD600/month with 3 shifts for 600 hours production.
- The material cost is not considered in order to focus on the performance and efficiency of the machine.